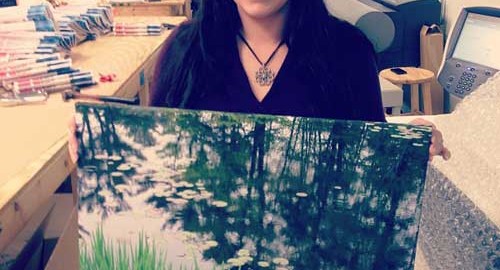
To ensure a fast and easy experience with Printkeg, or with any commercial printer for that matter, there are common occurrences that could cause order delays, missed deadlines or unexpected print results. A majority of customers need projects in hand as of yesterday – and we totally get that. When in a time crunch, it is important to properly prepare art files for printing, which is why Jessica created this no-no checklist concerning art preparation.
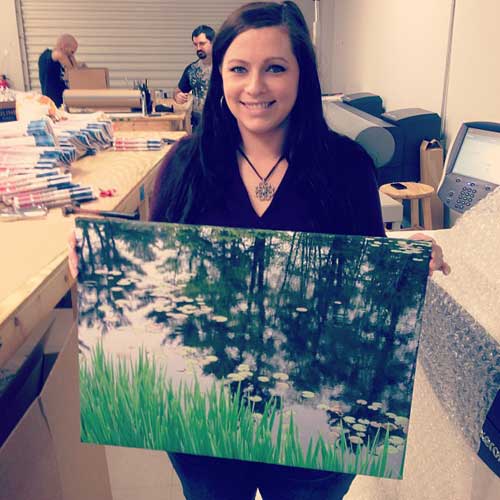
The following are the top 7 things NOT to do when sending art for print production.
1. Fail To Communicate With Us
For those who have specific instructions, please inform a customer representative. Staff designers cannot assume anything when dealing with customer files, so it is always best to over explain than under explain. Make sure to upload two art files if the final print product is to be double sided. If you do not want a white border around an image, please do not send the file with one. We offer custom cut sizes so please let us know if your file is not a size offered on our website. If you have a strict deadline (even if it is a week out), PLEASE let us know as sometimes orders get pushed back due to circumstances that are out of our control.
2. Use RGB Instead of CMYK
Most professional print shops print everything in CMYK mode. This is our default. Please convert all files to CMYK before sending over the file to ensure color accuracy. Most of the time if you send your file in RGB it will print a lot darker than intended. This is because CMYK, generally speaking, has a darker color scheme than RGB. Therefore, CMYK does not do well with neon/bright colors. Prints could also appear muted or inaccurate. For instance, RGB files using a bright blue color could print more purple in CMYK after conversion. If color accuracy is very important for your project, please request a physical sample. In most cases, colors do print accurately, but submitting RGB files can provide unexpected results.
3. No Bleed Area
Most print companies provide downloadable templates that include full bleed, or trim, areas. We require a quarter of an inch (.25) around every file to ensure edge to edge printing. Other print companies may vary in this requirement. For example, a 4.25″x6.25″ file would be submitted to print a 4×6 postcard. To prevent important text and images from being cut off, make sure to bring the text/image well within the recommend safety margin (a quarter of an inch from the edge of your canvas (safety dimensions = 3.75×5.75)). In many cases, we may automatically adjust artwork to print properly, but we can’t always save everything which could cause added time to turnaround.
4. Use Low Resolution Files
We strongly recommend 300 DPI or higher for optimal printing. Downloading an image from the internet will not work for print purposes since those images are typically saved as low quality 72 DPI images. Large sized images are certainly easier to work with, but it can be difficult to determine the resolution of an image without the proper software. If you are unsure about a file, feel free to email us your art before placing an order.
5. Send The Wrong Document Size
Sending the correct document size is very important and will ensure art is printed and shipped when expected. Do not simply assume that an 8.5×11 sized file will work for printing an 11×17 poster. Sometimes we can save files by stretching or adding backgrounds, but that requires time and could add to the turnaround time. Even worse, we may not be able to make adjustments appropriate for quality printing.
6. Add Crop Marks
Some print shops require crop marks added to the file; we do not. We use our own templates to send to the printer. Therefore we do not need crop marks on the file. Graphic designers and artists are trying to be helpful by sending them over, but sometimes (when not set up correctly) it actually makes the process more difficult for us, especially with booklets. We typically ask clients to resubmit artwork if crop marks are included which leads to unnecessary delays.
7. Wait Until The Last Minute
This is the worst, and most common, print sin of them all. Our entire staff understands deadlines can be tight and projects are important, but please try planning ahead by leaving a little wiggle room for any possible delays. As with all machines, sometimes our printers break down, and we cannot always get a technician to fix it the same day. Occasionally UPS will lose or damage a package requiring us to issue a reprint. Basically, we must all plan for unforeseen events especially with high importance projects. If your project requires a strict deadline, call or email us so we can note the account. We will do everything in our power to get your prints to you on time.
To ensure a fast and easy experience with Printkeg, make sure you resist the temptations of the above 7 deadly print sins. Provide us with clear instructions, send files in CMYK color mode, include bleed areas, ensure you are using a high resolution file, size files correctly, remove crop marks and give yourself enough lead time! By following these simple steps, you will stay stress free and build a great relationship with your print company (hopefully us)!
Thanks to all of our recurring customers. All of you are awesome and most of you turn in wonderful files.
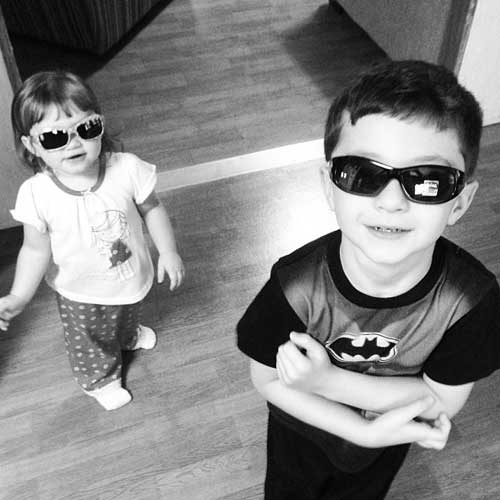